The Ultimate Production: Maserati's Factory Line
There are certain cities on earth that have become synonymous with the automobile - Detroit, aka Motor City, springs readily to mind. Stuttgart, Coventry, and Turin would also rank highly in this league table - but if one was considering top of the range cars there really can only be one answer, Modena. In and around this city many famous brands have flourished, Ferrari, De Tomaso, Pagani and Maserati, as well as many renowned coach builders and other automotive suppliers.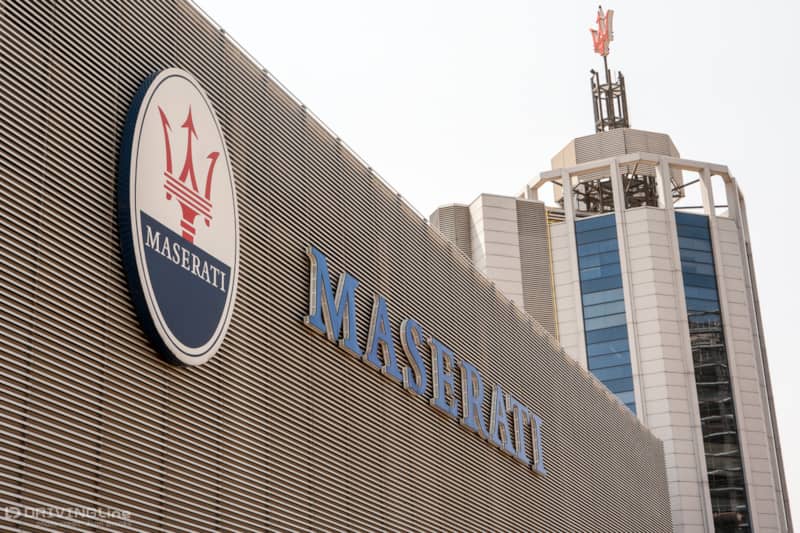
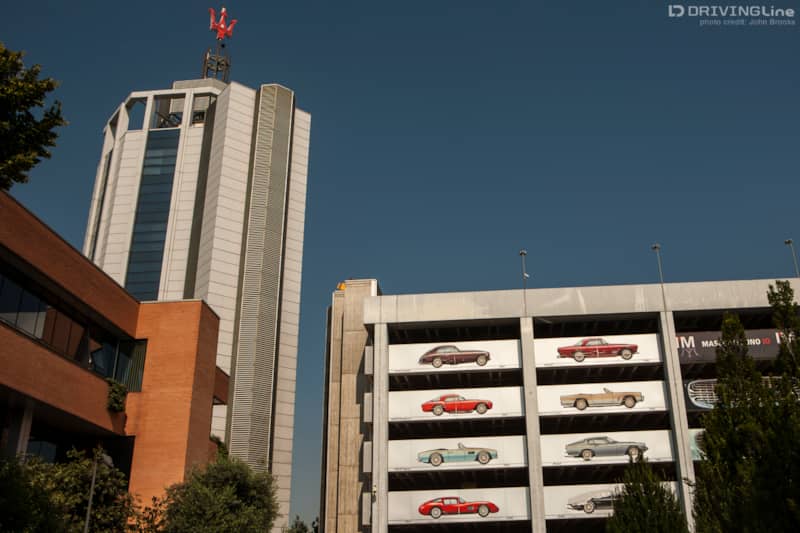
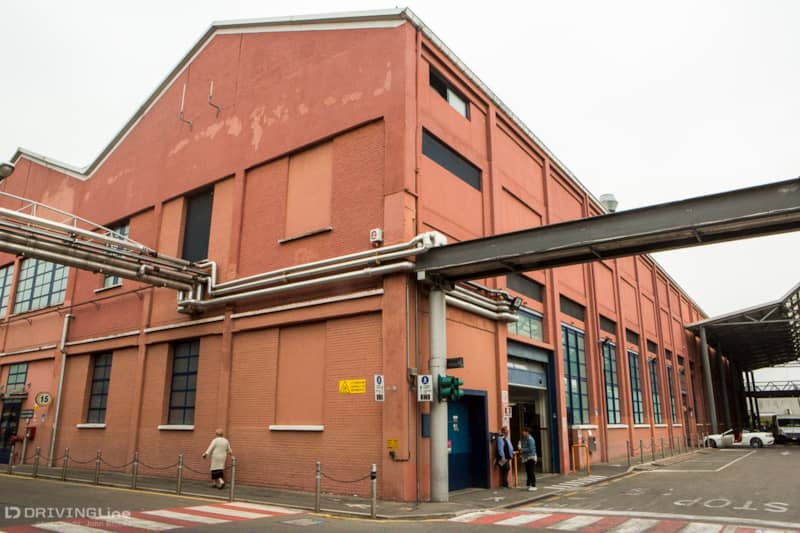
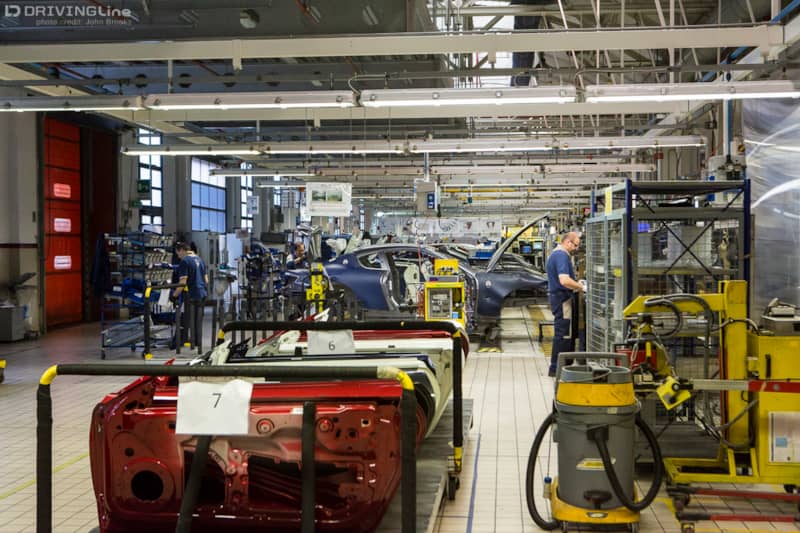
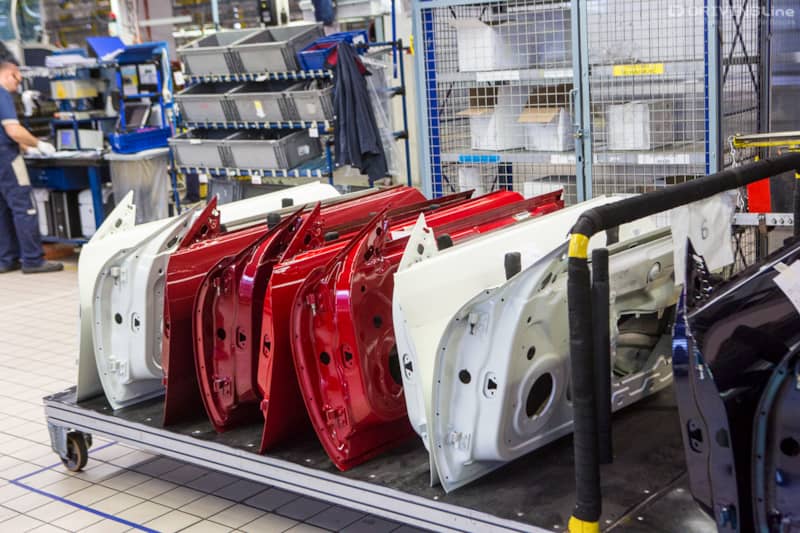
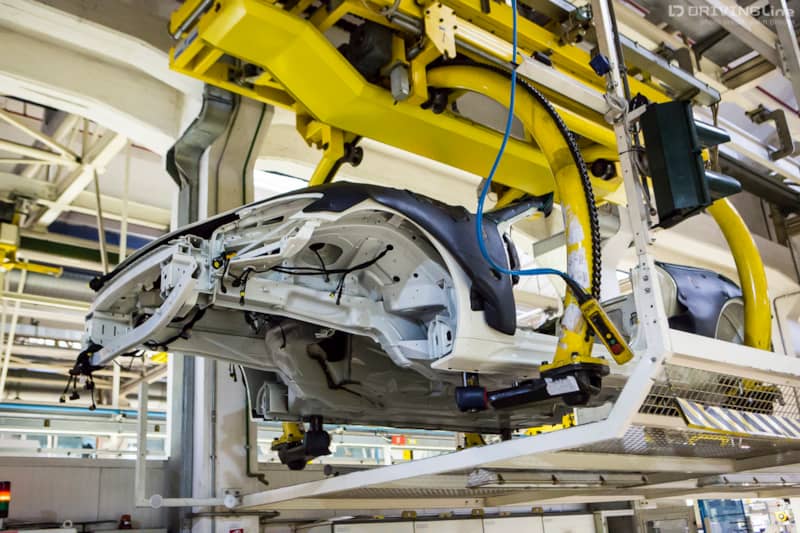
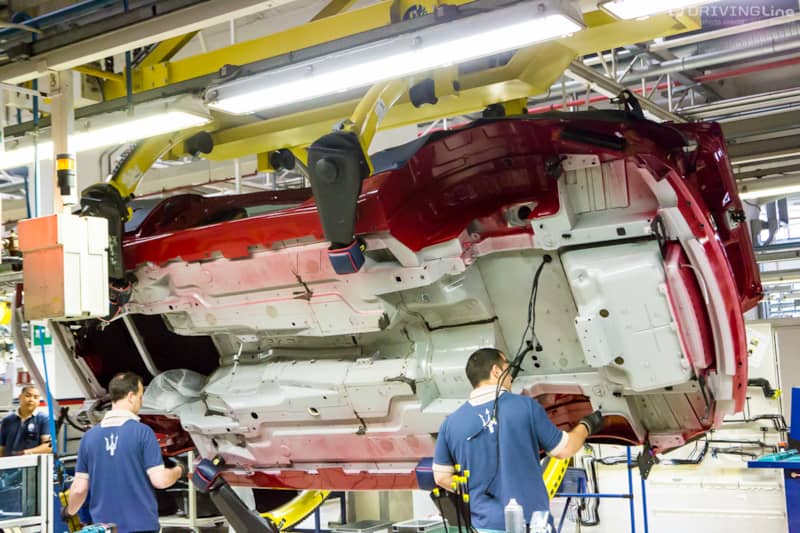
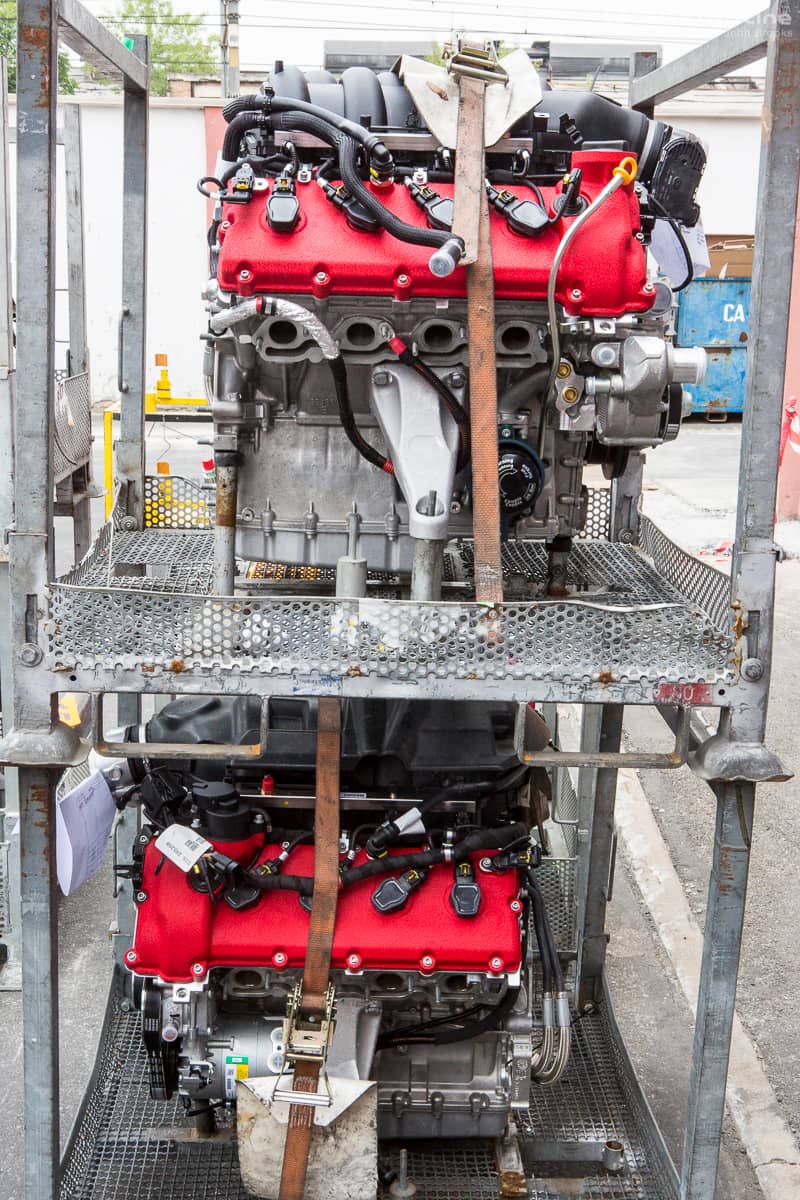
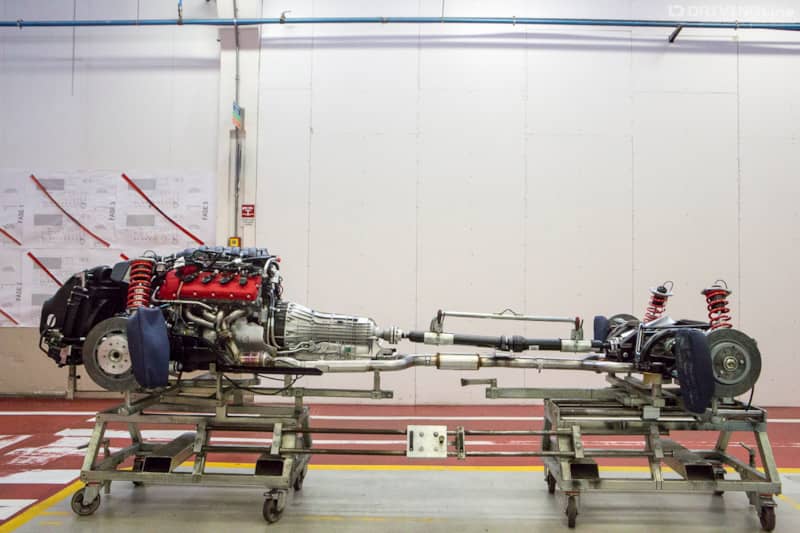
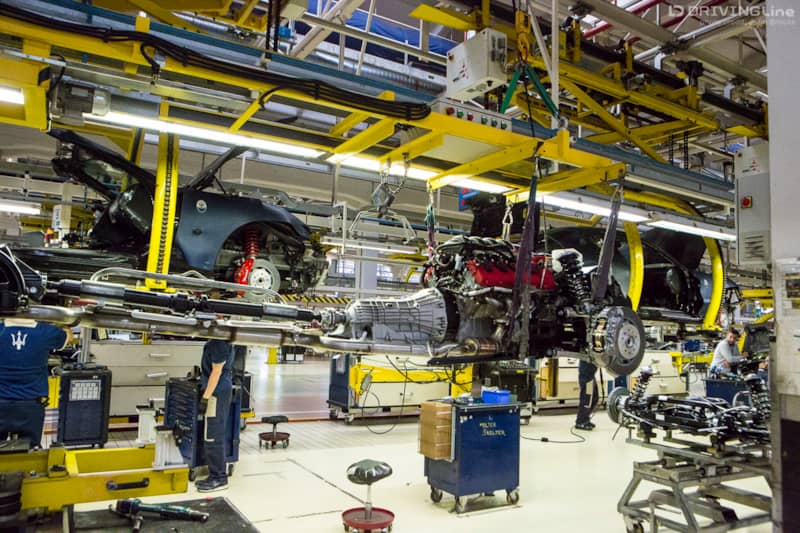
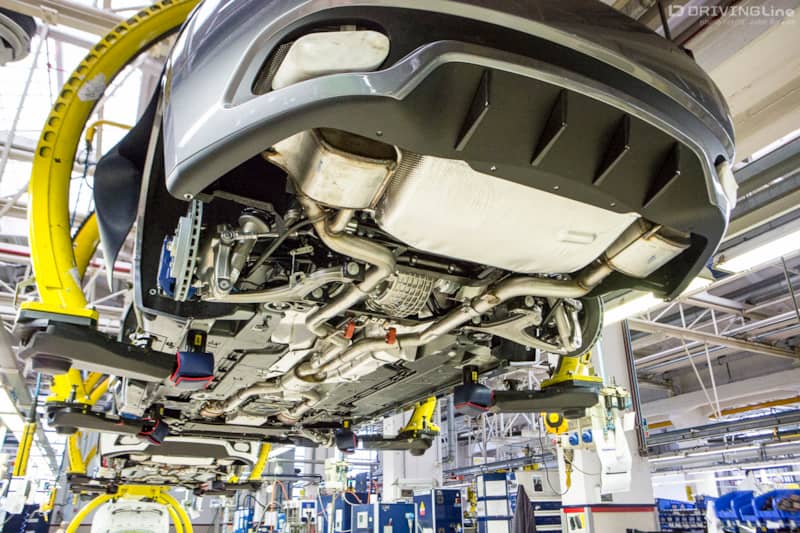
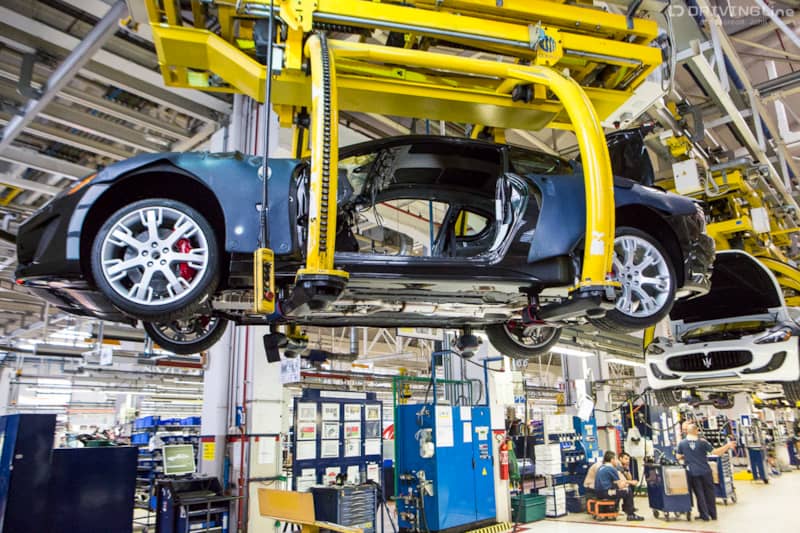
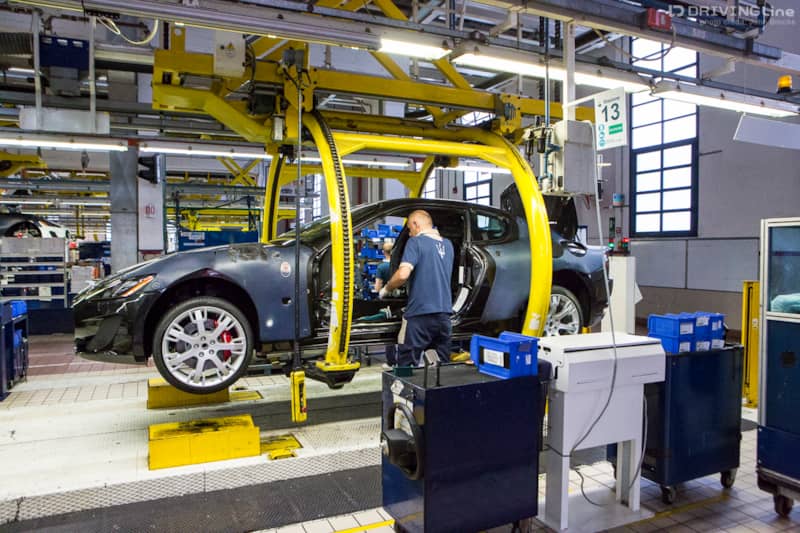

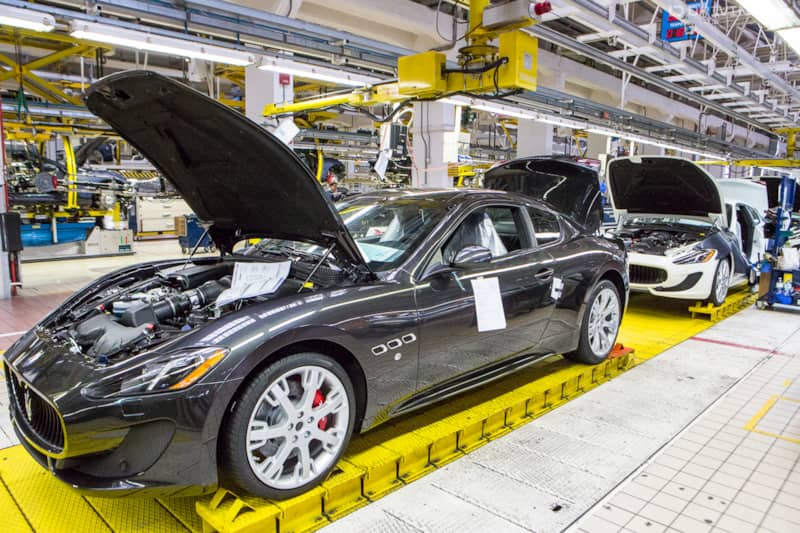
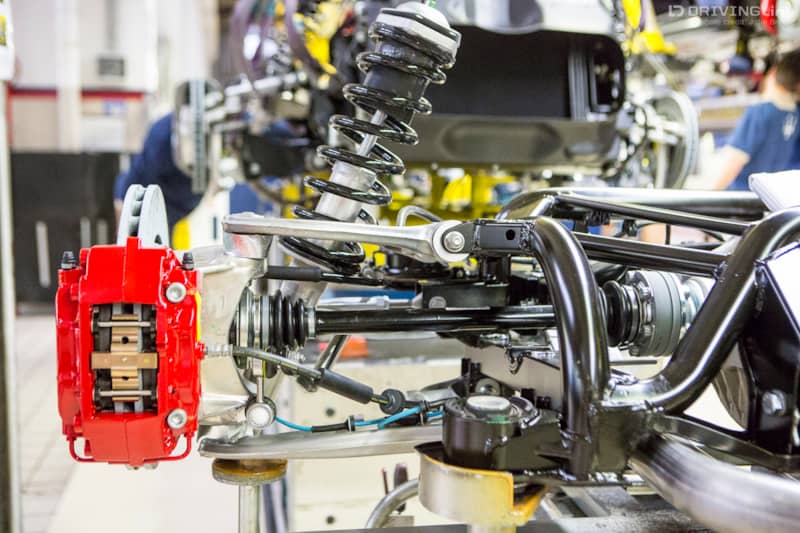
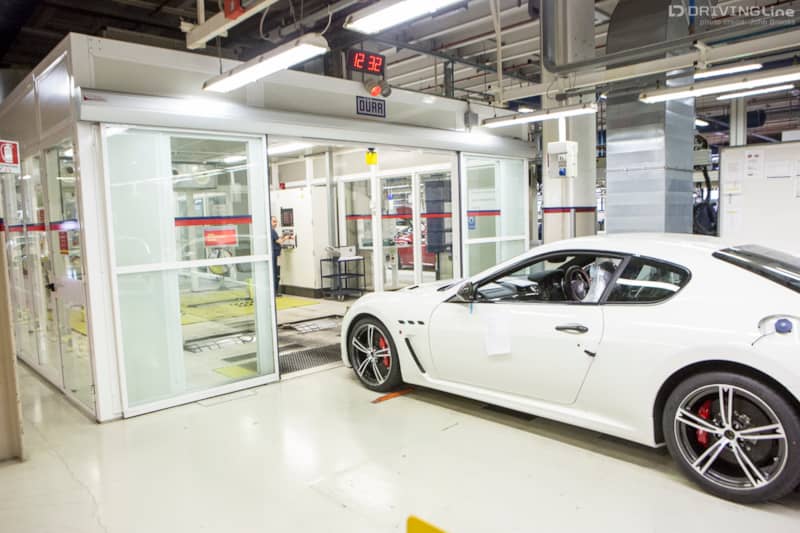
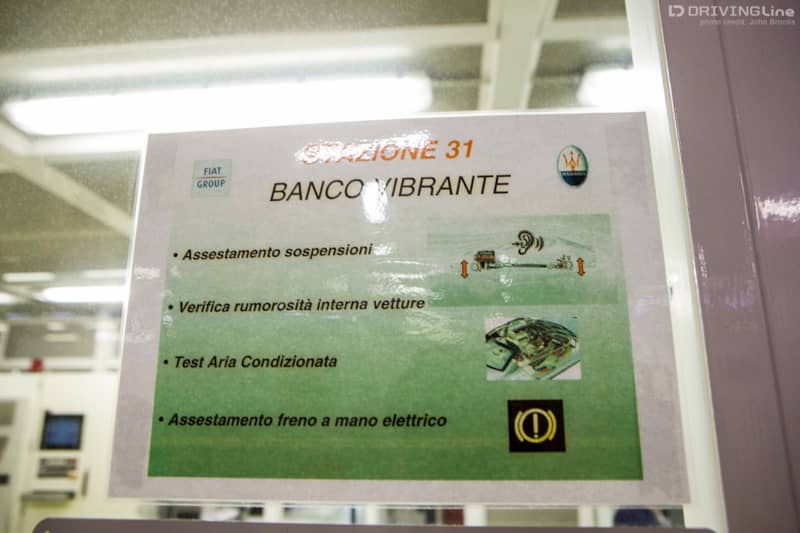
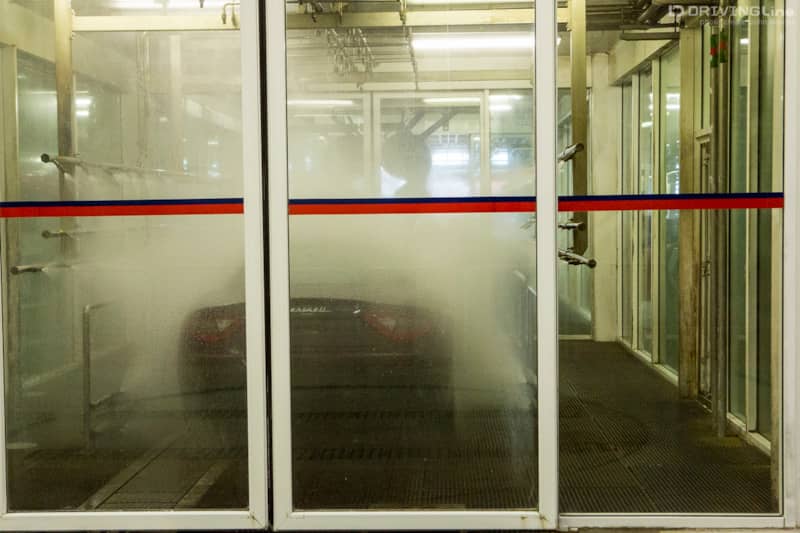
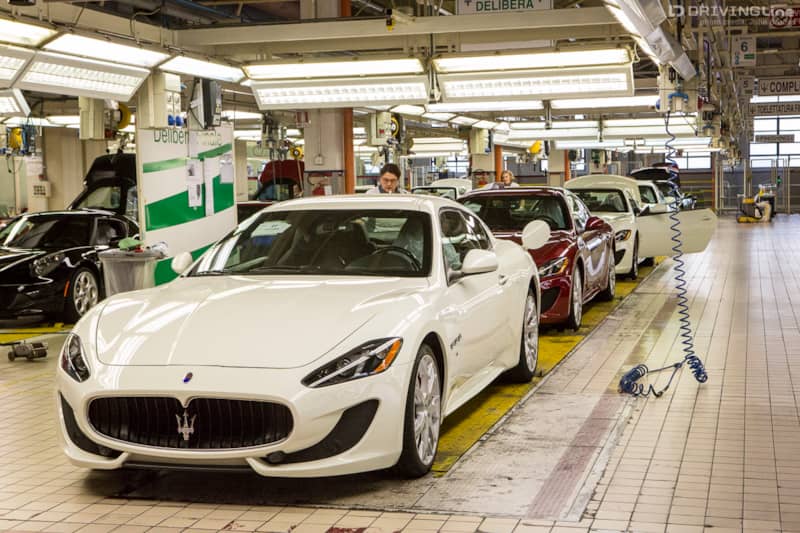
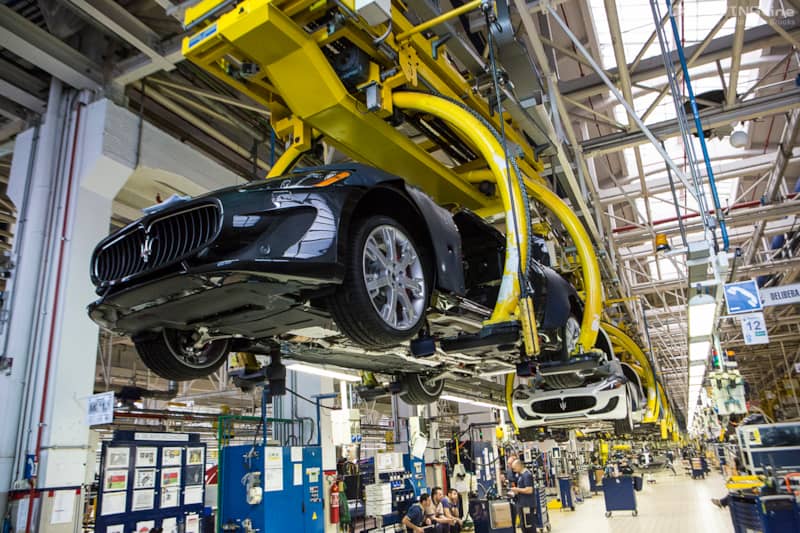